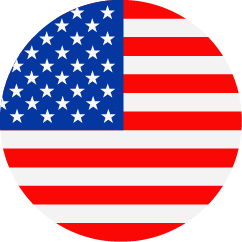
Change Control Coordinator- QS Specialist III
United States - New Jersey - ParsippanyQualityRegularDescription de l'emploi
Job Responsibilities:
- Responsible for managing change controls related to manufacturing product, process, equipment, facility, and computerized systems contributing to the oversight of key strategic, tactical, and operational goals..
- Independently review, initiate, complete, and thoroughly document critical, major, and minor change controls, managing local and global change controls and associated activities related to GxP operations. m
- Facilitate cross-functional meetings with stakeholders and leadership to ensure alignment with proposed changes and compliance to QMS expectations.
- Navigate through complex change review discussions, facilitating to a common decision for each change regarding approach and follow-up actions to be taken, and documenting the decisions and evaluations accordingly.
- Supports management and monitoring of change records for adherence to organizational or departmental metric targets, and maintenance of associated tracking tools/databases.
- Supports management review process through development and generation of quality system metrics and trending, and escalates issues as required.
- Supports the maintenance and improvement of quality systems processes, as needed.
- Works directly with operating entities and internal clients to ensure follow-up of change tasks.
- Participate in compliance audits as required.
- Maintains programs and processes to ensure high quality products and compliance with current Good Manufacturing Practices (cGMPs).
- Writes and/or implements changes to controlled documents (e.g., SOPs, Specifications, Methods, etc.) as needed.
- Provides guidance and technical knowledge to more junior staff, monitors the performance of daily tasks.
Knowledge & Skills:
- Will need to demonstrate the ability to manage multiple change controls of varying complexity and scope of tasks in a fast-paced environment to meet timelines.
- Demonstrates proficiency in Good Manufacturing Practices (GMPs)
- Demonstrates proficiency in application of QA systems principles, concepts, industry practices, and standards.
- Demonstrates thorough knowledge of FDA / EMEA standards and quality systems, and the interface with other functions like manufacturing, distribution and maintenance.
- Demonstrates Project Management abilities to lead and manage several projects, meeting deadlines and use critical thinking skills to problem solve effectively.
- Demonstrate strong scientific/technical understanding of small and/or large biologic molecule operations and related regulations/guidelines.
- Demonstrates knowledge of Six Sigma andLEAN concepts, and risk management tools for assessing change impact.
- Demonstrate knowledge and application of risk management principles, including identification, controls, mitigations, and actions.
- Demonstrates excellent verbal and written communication skills to all levels of the organization. Technical writing skills required.
- Demonstrate ability to problem solve and lead process improvements.
- Demonstrate ability to lead cross-functional meetings and make decisions as QA representative.
- Demonstrates strong interpersonal skills with ability to influence, negotiate, manage conflict, and negotiate.
- Demonstrates proficiency in Microsoft Office applications.
Education and Experience:
- 6+ years of relevant experience in a GMP environment for biologics manufacturing and a BS or BA, with change control experience a must.
- 4+ years of relevant experience and a MS.