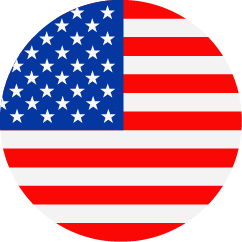
Director, Quality Systems
United States - Maryland - Frederick, United States - California - Santa Monica, United States - California - OceansideQualityRegularJob Description
We are seeking a Global Director for Quality Systems. This is a critical leadership role responsible for overseeing the strategic development, implementation, and maintenance of global quality systems and processes across our cell and gene therapy product manufacturing network. This role ensures the quality, compliance, and effectiveness of our operations through the management of key quality system elements, including change control, deviations, corrective and preventative actions (CAPA), training, and document control. The Director will provide technical expertise and strategic direction in quality systems to ensure robust and harmonized processes globally.
Job Responsibilities
Global Quality System Oversight:
Develop, implement, and manage comprehensive global quality systems and processes, including change control, deviation management, CAPA, training, and document control.
Serves as the primary point of contact and decision-maker for internal policies, procedures, and strategy documents governing core quality system elements across the global network.
Support in knowledge advancement beyond the Quality organization to build, maintain, and develop capabilities across the network for core quality system processes.
Develop knowledge-based programs to advance education and training programs related to these systems.
Provide mentoring leadership to stakeholder SMEs to build capability for new and existing sites or where gaps in technical expertise have been identified.
Sponsor and oversee activities focused on driving process improvements and harmonization projects across the network for change control, deviations, CAPA, training, and document control.
Serve as the SME leadership role for topics associated with change control, deviations, CAPA, training, and document control across the network, representing on network teams and other appropriate governance forums.
Provide technical support during new process design and facility start-up activities to ensure quality system requirements are integrated at the sites.
Engage in providing support during regulatory submissions and on-site inspections related to quality systems.
GMP Compliance and Quality Control:
Ensure all quality system processes comply with current Good Manufacturing Practices (cGMP) and relevant regulatory guidelines (e.g., FDA, EMA).
Provide guidance on developing and validating quality system processes and associated documentation.
Provide technical support for investigations related to deviations and CAPA to help identify root cause and implement effective corrective and preventative actions. Share best practices/learnings across the network.
Oversee the development and implementation of global training programs on quality system requirements.
Ensure the establishment and maintenance of a robust global document control system.
Cross-Functional Collaboration:
Provide technical expertise in quality systems to cross-functional teams, including Manufacturing, Quality Assurance, Process Development, and Regulatory Affairs.
Participate in the development and improvement of manufacturing processes, ensuring robust quality system controls are integrated.
Interact with regulatory agencies and provide quality system expertise during inspections.
Stay current with the latest advancements in quality systems management, regulatory expectations, and cell and gene therapy manufacturing.
Basic Qualifications:
PhD in a scientific discipline, engineering, or a related field with 8+ years of progressive experience in Quality Assurance within the pharmaceutical or biotechnology industry, with a significant focus on quality systems management in a sterile manufacturing and advanced therapies environment OR
Master’s degree in a scientific discipline, engineering, or a related field with 10+ years of progressive experience in Quality Assurance within the pharmaceutical or biotechnology industry, with a significant focus on quality systems management in a sterile manufacturing and advanced therapies environment OR
Bachelor’s degree in scientific discipline, engineering, or a related field with 12+ years of progressive experience in Quality Assurance within the pharmaceutical or biotechnology industry, with a significant focus on quality systems management in a sterile manufacturing and advanced therapies environment OR
Associate’s degree in scientific discipline, engineering, or a related field with 14+ years of progressive experience in Quality Assurance within the pharmaceutical or biotechnology industry, with a significant focus on quality systems management in a sterile manufacturing and advanced therapies environment OR
High School Degree with 16+ years of progressive experience in Quality Assurance within the pharmaceutical or biotechnology industry, with a significant focus on quality systems management in a sterile manufacturing and advanced therapies environment.
Preferred Qualifications:
Advanced degree in a scientific discipline, engineering, or a related field.
Minimum of 10 years of progressive experience in Quality Assurance within the pharmaceutical or biotechnology industry, with a significant focus on quality systems management in a sterile manufacturing and advanced therapies environment.
Experience with cell and gene therapy manufacturing processes and associated regulatory requirements.
Prior experience in a global role with responsibility for quality systems.
Experience with electronic quality management systems (eQMS).
Experience in leading and managing direct reports and cross-functional teams.
Demonstrated ability to effectively collaborate with and influence stakeholders at all levels of the organization, including senior leadership.
Extensive knowledge of cGMP regulations, FDA/EMA guidelines, and industry best practices related to quality systems in cell and gene therapy manufacturing.
Strong expertise in the principles and application of change control, deviation management, CAPA, training program development, and document control systems.
Proven experience in developing, implementing, and maintaining global quality systems.
Excellent leadership, communication (written and verbal), and interpersonal skills.
Strong problem-solving, analytical, and risk assessment skills.