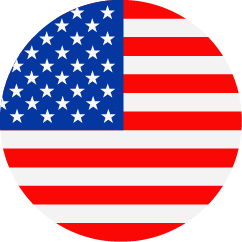
Manufacturing Maintenance Planner
United States - California - La VerneFacilities Operations/EH&SRegularJob Description
Gilead Sciences, Inc in La Verne, California is seeking a planner for maintenance that has a minimum of 3 years of experience who can plan maintenance activities to avoid delays, improving productivity and workflow and reducing maintenance costs.
The following functions are considered essential for successful performance in this job description:
- As a planner for maintenance activities, you will be part of the maintenance team and perform the necessary preventative maintenance programs for the La Verne Pharmaceutical Facility.
- Respond to maintenance emergencies in all La Veren’s facilities as quickly and efficiently as possible.
- Potentially work with construction and maintenance contractors to ensure the facility integrity.
- Work is performed based on job plans scheduled through Maximo.
- Good written skills are necessary to properly fill out preventative maintenance activities and plan the work.
- Works may be independently or with others on different projects.
The following are key responsibilities for the planner position:
- Understand the job well enough to describe what needs to be accomplished, estimate labor hours, tools and resources needed to complete different work orders.
- Prepare preventative maintenance plans and schedules that are in sync with the organizations’ maintenance goals.
- Constantly adjust schedules to account for emergency work.
- Act as the primary liaison person between maintenance and operations.
- Lead communication between maintenance and other internal beneficiaries of maintenance work to ensure that everyone receives timely, efficient, and quality service.
- Coordinate planned downtimes to reduce mean time between failures and minimize interference with production schedules.
- Minimize the number of interruptions once work begins.
- Establish job goals for the maintenance workforce.
- Provide immediate insights into potential labor shortages.
- Help with keeping an optimal stock of spare parts and materials.
Knowledge requirements:
- High School diploma or equivalent plus a minimum five (5) years’ experience supplemented by studies or other vocational school OR Associate degree plus a minimum of four (4) years of experience.
- Three years minimum in planning / scheduling experience
- Experience in MRO (Maintenance, Repair and Operating materials) inventory management experience.
- Must have computer skills and knowledge with MS Work, Excel, Outlook and PowerPoint.
- Must have experience using Computerized Maintenance Management System.
- Must be able to be periodically “on-call” on designated weekends and holidays and available on-site during plant shutdowns/start-ups, plant commissioning and decommissioning activities, and other operational events, planned and unplanned, when required.
- Good understanding of GMP environment is a necessity.